By Matthew Koehler
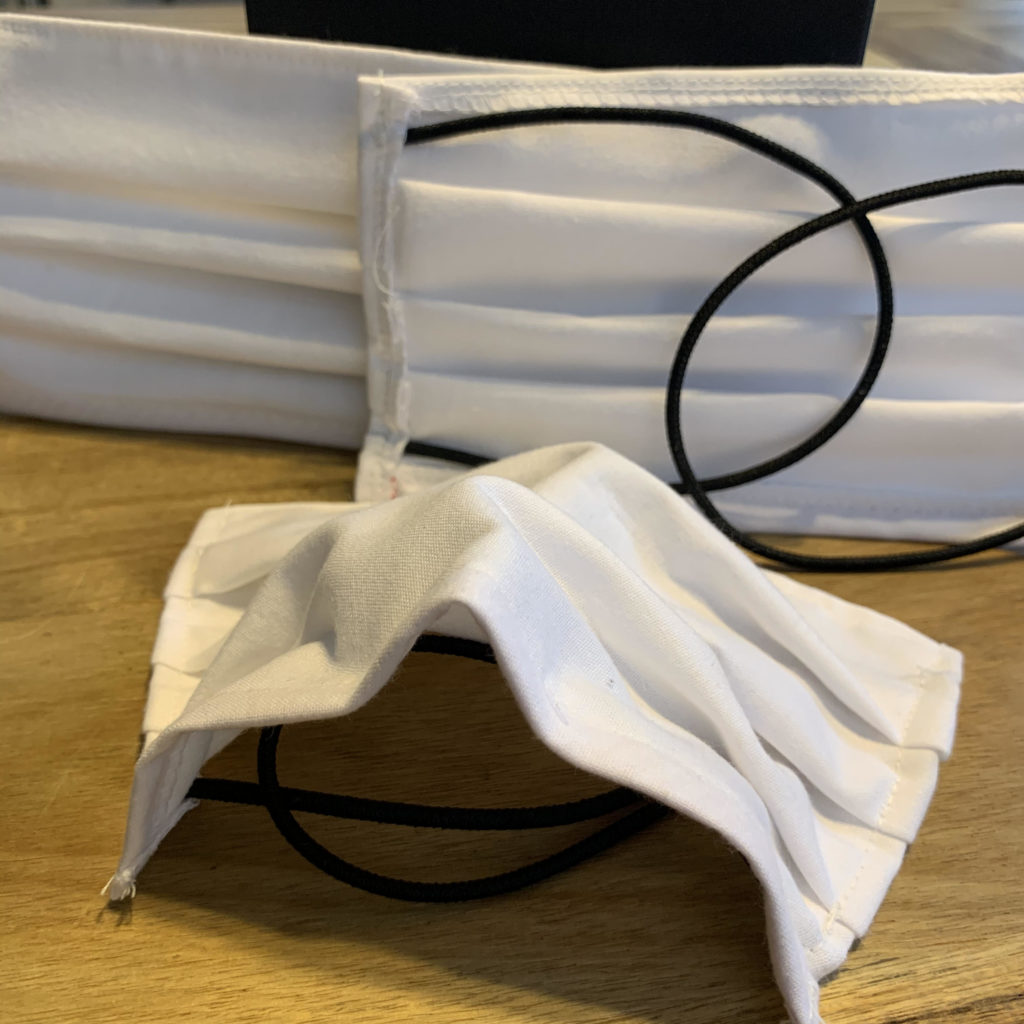
to first responders, staff around the Wharf,
and passersby; Courtesy of The Press
At the beginning of March, when the threat of a global pandemic at home still seemed remote, and the dire news from abroad had not yet pushed national leadership to action, Dianne Lee and her husband Je Kang, owners/operators of The Press dry cleaning at the Wharf, heard from affiliates on the West Coast that the threat was real. They were hearing about the drop in revenue, people not showing up for work, layoffs, and especially shortages in personal protective equipment, or PPE. Specifically, there was, and still is, a nationwide shortage of masks for frontline workers
As professionals in the garment care industry, they were perhaps in a unique position to do something about the shortages of masks, at least as it pertains to Southwest and the rest of the District. “You’re one of the first people to actually ask me this, and this is a real cool story,” Dianne Lee told me over the phone.
“We’re a part of America’s Best Cleaners, which is the most stringent accreditation for the garment care industry. We’re technically paying them a monthly fee for them to tell us how bad we are. [B]ut, the benefits that come along with it is that they [are] able to host a weekly discussion. [T]hey were just telling us things that we couldn’t even imagine. And this was about over 5 weeks ago (from our April 10 phone call) because we started making masks three weeks ago. When they told us there was a shortage [of] masks, we started making masks.”
Dianne Lee officially got into the dry cleaning business 10 years ago when she and her husband took over the business from his family, who had been in the game for more than 40 years. Their first retail location was on Capitol Hill where they built a solid reputation by word-of-mouth. They were also the only dry cleaners open seven days a week, which she says really set them apart. “He loved the whole D.C. local community,” Dianne said of her husband, “everyone was just super supportive.” They now have four retail locations and deliver to over 200 residential and commercial properties.
What does a dry cleaner have to do with making masks? Well for starters, when thinking about industries that could be converted or repurposed to perhaps make PPE’s, a dry cleaner with training and knowledge in fabrics, including a professional seamstress, is not that much of a stretch.
According to Dianne, who spoke on behalf of her husband, it seems their business, or him personally, were perfect to take on this initiative. “This is kind of ironic. He studied biology [and] he actually specialized in rare and infectious diseases.” Specifically, Lee said Kang did not study the family of coronaviruses, but “that kind of background made him a lot more cautious and conservative [in] dealing with packages.” Lee stressed that in taking on this initiative, her husband was very adamant about following the CDC guidelines about making, washing, and disinfecting the masks, “He was very very strict on that.”
How many masks do they make and what specifically do they make the masks from? At the time of our interview, Lee told me that they were up to 100 masks a day. They are made with muslin fabric, which is 100 percent cotton, and usually used for wedding gown preservation. Their in-house seamstress makes them and Lee has been handing them out to security officers, custodial teams, first-responders – anyone they see on the streets. “We’ve been visiting local fire stations, police stations…[a]nd just dropping off the masks and offering free delivery to their stations…”
Why do this at a time of unprecedented economic constriction? Lee stresses that her husband wants this initiative to be more about community and service, not money, which is why they have declined to take any money for the masks, even for the cost of production. He’s “been really adamant that everyone who needs a mask can get one.” They’ve had offers from companies to put their logo on the masks but Dianne reiterates that her husband is doing this as a community service and doesn’t want anything artificial on the masks “keep it as natural as possible.”
“[It’s] also getting our name out there, you know. A lot of people out there, our regulars, have bought $500, or $1000 in prepaid dry-cleaning credits from us so we can keep this initiative going, too. Or keep our staff… to do stuff.”
With economic hardships in mind, and millions of layoffs heavily concentrated in the hourly/minimum wage sector, I asked Dianne whether or not they have had to make some hard decisions about downsizing. “We’re really trying to use this time to cross-train people instead of lay them off because we want to give them the option [to stay employed]. If they want to take off or file for unemployment… We’re trying to help them as much as we can.” At the time of our call, she was out finishing deliveries with one of their employees.
She told me that they had to reduce pay, but that they are still paying their employees above the minimum wage. “We paid our employees better before, and when we had to do the wage reduction… I think more people were worried about getting their families sick, but we’ve actually kept on most of our employees. Almost all of them,” she added.
“Our team, drivers, have been driving to homes and even delivering groceries. We’ve dropped off lysol and toilet paper.”
So, has the initiative been successful?
At first, she says people were resistant to the idea of the masks, especially given early guidelines from the CDC, which did not suggest the wide use of masks for uninfected or non vulnerable people. They were meant more for people who were at risk or already sick, so they would have less of a chance to transmit the disease. There were also concerns that people would reuse the masks without washing or disinfecting them, which can lead to bacteria growing on them and making people more sick. Furthermore, at the beginning of the social distancing measures there was a concern that people would rely on the masks too much and not practice social distancing.
Initially, the masks The Press made were one-time use only – for essential personnel who didn’t have time to wash or disinfect them, but as their usage became more widespread to the general public, Dianne says they expanded the types of masks they were making and people were less reticent to accept them
“We had been making surgical masks, but now we’ve seen that there’s been [more of] a need from the community, right? We want to [save] the N95 masks for the hospitals. We want to save the surgical masks for the hospitals. Now [we’re] making two different kinds of masks. We still make our surgical masks with the twist ties on top for first responders. And then we’re making cotton masks without the twist ties.”
The twist ties at the top N95 masks make a more complete seal, which is necessary for people working in high risk/high exposure jobs, but aren’t as necessary for going to the store or walking around outside. Masks they hand out to the general public don’t have the added twist ties, which makes them machine washable. She tested hers out in the washing machine (at the highest temperature you can) and it came out just fine.
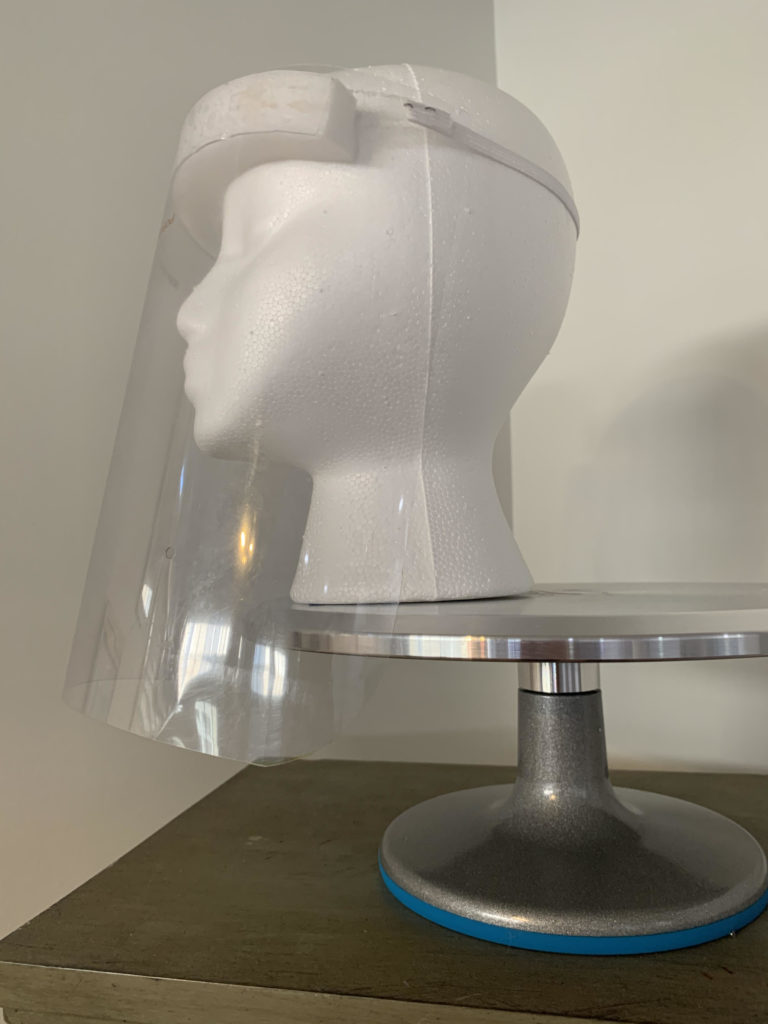
part of their new community initiative; Courtesy of The Press
To date, they have given out over 3,000 masks and are now working on building face shields – one made of plexiglass, which is their next initiative (see photo). They won’t be able to make as many face shields as facemasks but want to be able to donate those to any hospital employees.
Before ending our interview, I asked Dianne if she had any advice for the community. “Definitely try to stay home. We always try to get our information from the CDC, right? We [are] able to use our ADC/ABC affiliation and study everything that’s going on in Seattle, and that’s what we’re still doing. [So] we’re seeing all these trends in Europe, even in China where [the curve] might’ve flattened, but people are still worried that a second wave could come… We’re just trying to really encourage people to stay home. Only use a mask when going to get essential groceries, or things like that.”
She also pointed out that with the increase in hand washing and use of sanitizer to use moisturizer “because people are getting really dry, chapped skin on their hands, and those can be crevices for bacteria too.”
A final word of warning on washing clothes or sending them to the dry cleaners, especially given the highly contagious nature of COVID-19. We are likely all doing a lot of laundry right now, which is necessary, but it’s important to do it the right way. According to experts, certain fabrics like polyester may preserve the virus longer than others fabrics like cotton. Washing clothes via standard methods – some detergent, hot water, and some time in the dryer – is not enough. A combination of high heat and a disinfectant, like a detergent with a bleach compound, will be more effective at eliminating the virus.
“Dry-cleaning does not kill all pathogens [emphasis added], and we’ve seen dry-cleaners with a horrible horrible, like, advertisement saying dry-cleaning will kill viruses and COVID-19. And, we’re totally against that.” Dianne explained that they use a different process in addition to dry cleaning. Their garments are quarantined in an O2 room for more than 24 hours, which is longer than CDC guidance. Ozone has long been used in the dry cleaning process to deodorize garments. “We always say, ‘We’re your garment care specialists, we’re the professionals. We don’t want to give you any false information.'”
With that in mind, if you find yourself in need of some dry cleaning, maybe ask about their process first.